NOTE:
While great efforts have been taken to provide accurate and complete information on the pages of CPEP, please be aware that the information contained herewith is considered a work-in-progress for this thesis project. Modifications and changes related to the original building designs and construction methodologies for this senior thesis project are solely the interpretation of Shane Flynn. Changes and discrepancies in no way imply that the original design contained errors or was flawed. Differing assumptions, code references, requirements, and methodologies have been incorporated into this thesis project; therefore, investigation results may vary from the original design. |
|
 |
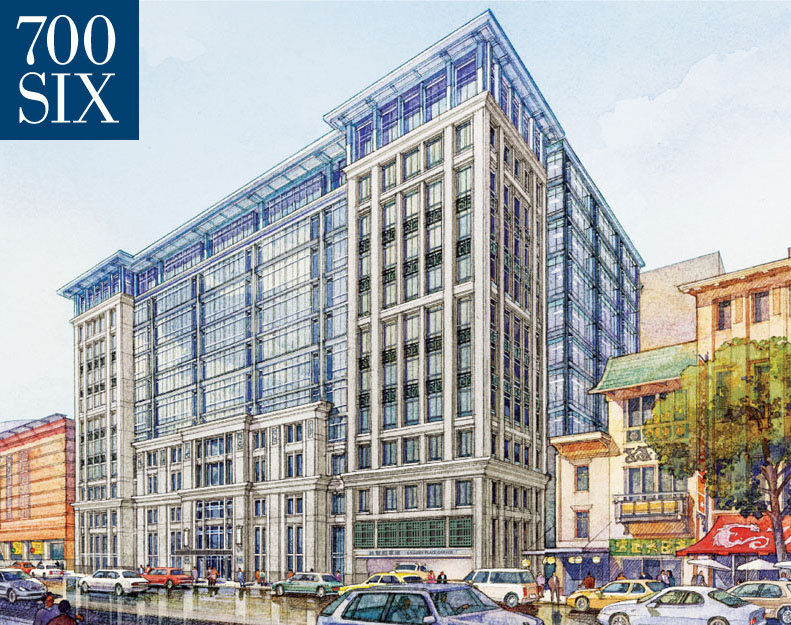
Building Statisitcs Part 1
General Building Data
Building Name: 700 6th Street
Location and Site: 700 6th Street, Washington, DC
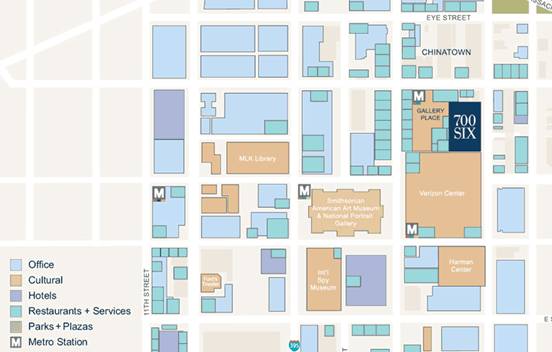
Building Occupant Name: Main Occupant: Cadwalder
Occupancy Type: Office Building
Size: 318,000 Square Feet
Number of Stories: 12
Primary Project Team:
Owner: Akridge Real Estate Services
http://www.akridge.com
General Contractor: Balfour Beatty Construction
www.balfourbeatty.com
Architect: Hellmuth, Obata + Kassabaum, Inc.
http://www.hok.com
Structural Engineer: Cagley Associates
www.cagley.com
MEP Engineer: Girard Engineering
www.girard.com
Civil Engineer: Bowman Consulting
www.bowmanconsulting.com
Dates of Construction: Start: April 2nd 2007
Finish: November 2009
Total Construction Cost: $46,450,000.00
Project Delivery Method: Design-Bid-Build
Architecture
Architecture:
At the center of downtown Washington 700 Sixth Street is a classically-designed, modern office structure with all the attributes and amenities demanded by businesses today. 700 6th has over 300,000 square feet of office space with efficient floor layouts to maximize the user’s needs. There is a 4 level parking garage directly below the building accommodating commuters that do not use the Metro. The main lobby has marble flooring, glass bridges, and metal walls. This is a LEED Platinum rated building with the largest Commercial Office Building Green Roof in DC.
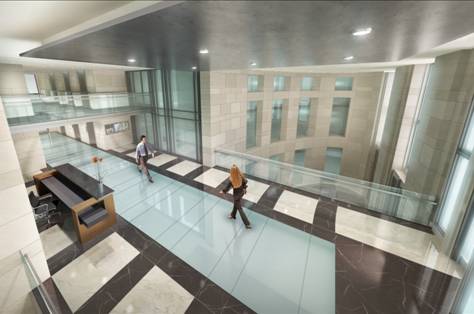
- Virtually free standing building with upper-floor windows on all four sides
- Classic architectural design by HOK
- Voice/data–fiber optics and T1
- Floor load–80 lbs. live load, 25 lbs.
- Electric power–2.5 watts per square foot for lighting; 6.0 watts per square foot for power receptacles
- HVAC–variable air volume system
- 1 space per 1,700 SF in 3-level secure parking garage
- Finished ceiling height of 8’6’’ on all office floors
- Column spacing–30’x30’
- 6 high-speed, traction passenger elevators serving office floors
- 2 high-speed garage shuttle elevators
- State-of-the-art security system
- Reinforced concrete base building construction
National Model Codes:
- The District of Columbia Construction Codes, 1999 Supplement
- Accessibility Code
- BOCA National Building Code, 1996
- National Electric Code,1996
- The BOCA National Fire Prevention Code, 1996
- International Mechanical Code, 1996
- International Plumbing Code, 1995
Zoning: B, M, A-3, S-2
Historical Requirements: Not Applicable
Building Enclosure
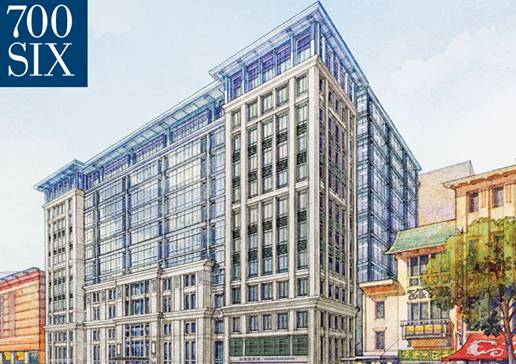
Building Facades:
The exterior of 700 6th Street is made of 6 different materials.
- EIFS
- On wall facing Gallery Place (Refer to Location and Site Map)
- Curtain Wall
- Punch Windows
- Decorative Concrete Masonry Unit
- Lightweight concrete
- 4 inch width
- Split face finish
- The color matches the Alabama limestone
- Limestone hand set
- Alabama Limestone that is hand set from the 1st to third floor
- Pre-cast with Alabama Limestone casted into pre-cast
- Goes from 4th to 12th floor
- Pre-cast
- Concrete with similar color to match Alabama limestone
- Metal spandrel panels
- Niko Panels
- Rein Zink material
- Hand bent metal
- Hand set on curtain frame
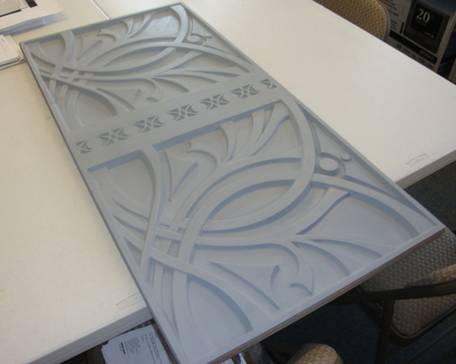
Roofing:
The 700 6th Street building has the largest Commercial Office Building Green Roof in DC. The Green Roof has 2 levels (upper and lower). The bottom level has a wood flooring area for observation and the rest of the level is green. The HVAC equipment is concealed on the bottom level of the roof. The upper level is not assessable to the public and is completely dedicated to being Green. Refer to the attached picture to see the difference between the upper and lower levels.
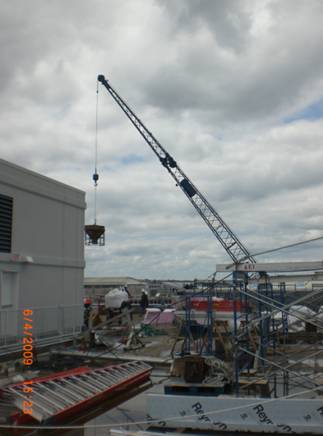
Sustainability Features
- LEED Platinum rated building
- Green Roof
- Largest Commercial Office Building Green Roof in DC
- Water Conserving Fixtures
- Low flush urinals,
- Aerated faucets and showerheads (lower flow with air providing the pressure)
- Dual flush valve toilets
- Dual flush valves give users the option of using a full or half flush by pushing the lever up or down
- 700 Sixth Street uses no CFCs or HCFCs, thereby preventing ozone depletion
- Over 75 percent of all construction and demolition debris is being recycled, salvaged for reuse, or otherwise diverted from landfill.
- Recycled content will comprise over 10 to 20 percent of building materials
- Regional materials will comprise more than 10 to 20 percent of all building materials
- Certified Wood
Building Statistics Part 2
Structural
The main superstructure of the building consists of cast-in-place concrete. Cast –in-place concrete was used for building footings, foundation walls, grade beams, slabs-on-grade, suspended slabs, concrete toppings, and columns. All the above features used normal weight concrete. The column spacing is 30’ by 30’ with a finished ceiling height of 8’-6”. The typical slab thickness is 9” with a thickened slab thickness of 16.5” at columns. All columns are typically 24”x 24”. All the formwork used typical wood framing. The formwork is removed, cleaned, and reused. A pump truck and crane bucket was used for all major pours.
Column Formwork

Suspended Slab Formwork
Mechanical
The main mechanical is located on the penthouse floor plan. The penthouse has floor plan has 3 cooling towers and an emergency generator. Also located on that floor are a Mechanical Engineers room and a mechanical room. Each individual floor has its own mechanical room located in the core of the building. There is a total of 25 Air Handling Units located throughout the building. Each air handling unit on average has the capacity of 9000 CFM and runs on 460 Volt 3 Phase motors. The 3 cooling towers have an average capacity of 1100 GPM’s that run on 460 Volt 3 phase motors. The HVAC is a variable air volume system. The AHU’s distribute through galvanized sheet metal duct and supplied to rooms through registers and grilles. The fire protection system consists of a wet pipe sprinkler system.
Electrical
700 6th Street has on average 6.0 watts per square foot for power receptacles. Each floor contains a 150 KVA, 480-208/120V/3 Phase dry-type transformer. The P-1 level contains multiple transformers ranging from 15 KVA to 75 KVA. Level P-1 contains 3 switchboards that are rated to withstand a fault current of 300,000 Amps. Emergency/standby power will be supplied by a 500 KW diesel engine generator.
Lighting
2.5 watts per square foot is the average power for lighting for 700 6th Street. There are 36 different types of lights used on this building. The different types of lighting fixtures are fluorescent, metal halide, and L.E.D. Most of these fixtures run off 277 volts and the rest run off of 120 volts. The lights are all mounted differently, there are; surface mounted, semi-recessed and recessed. Only the core, parking levels, and lobby are fitted with lighting fixtures. The rest of the building is left for the owner to fit out.
Additional Engineering and Engineering Support Systems
Support of Excavation
- Sheet piles and lagging were used for excavation support.
Pile Driver
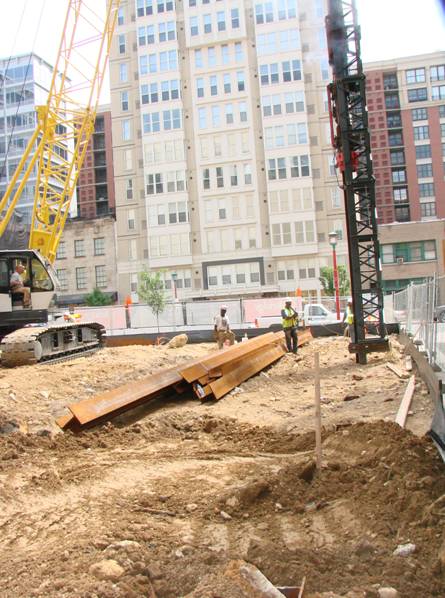
Sheeting and Shoring
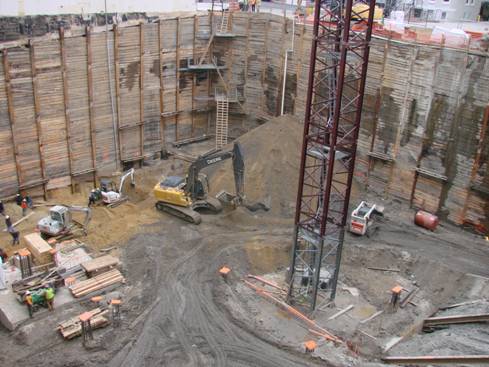
Bracing
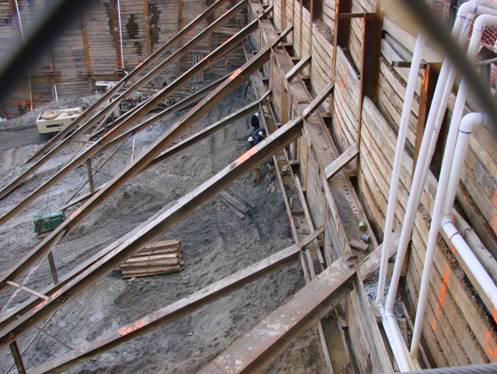
Tiebacks
Demolition Required
- The 5 story building shown below needed to be removed in its entirety.
- Below the building is a 3 level parking garage that needed to be demolished
- The 1 level red building needed to be demolished.
- Asbestos and Lead paint was not found in this building
Existing Building to be removed
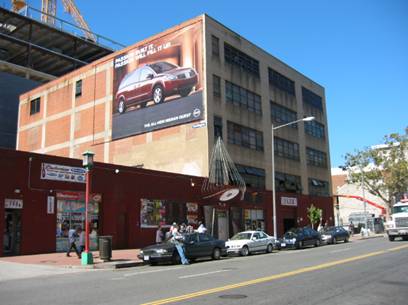
3 Level Parking Garage
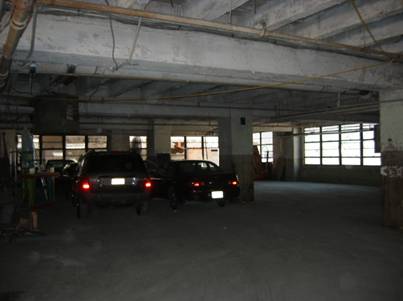
|
|
|
|
|
CPEP Site is Complete and Ready For Review
|
04.26.10 |
Reflections and ABET form Posted |
04.19.10 |
|
04.26.10 |
|
|
Thesis Presented/Presentation Posted |
|
|
|
|
|
|
|
|
|
|
|
|
|
Building Statistics Part 2 Posted |
|
|
|
Building Statistics Part 1 Posted |
|
Owners Permission Recived |
|
|